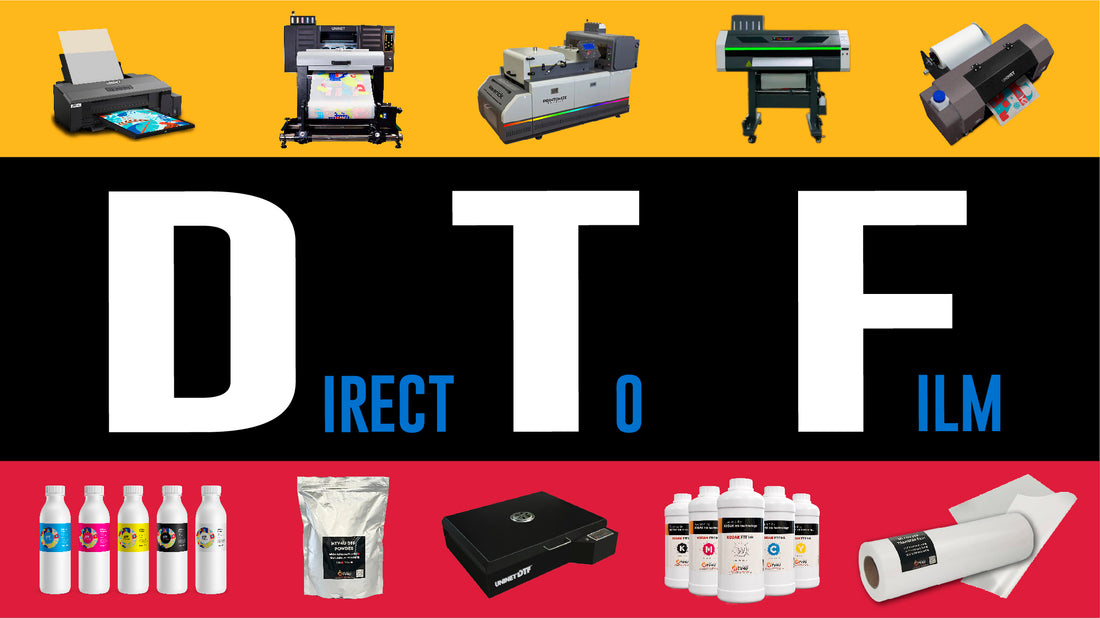
What You Need to Know about Direct-to-Film (DTF) Printing
Share
Direct to Film Transfers (DTF): The Future of Textile Printing
If you’ve been working in the printing industry, you've probably heard of the Direct to Film (DTF) nowadays. Currently, DTF is a relatively new printing technology but one of the most versatile techniques available in the print industry. DTF differs from the DTG method in that it is not limited to cotton fabrics and can effectively be used on both cotton and poly blends. This is why this printing technique is becoming so popular.

DTF transfers are an innovative approach to textile printing that offers superior quality and versatility compared to traditional printing methods. DTF printing technology has become increasingly popular over the past few years, and it is expected to be the future of textile printing. Whether you're a small or large textile business, adopting this technology can significantly improve your print quality, speed, and costs. In this article, we will discuss what DTF printing is, how it works, and its advantages over traditional printing methods.
What does DTF mean?
DTF stands for Direct-to-Film. In the context of textile printing, DTF refers to a printing process that uses a special DTF printer to print designs directly onto a clear film. The design is then transferred from the film onto the textile using a heat press. The end result is a high-quality, full-color print that is durable, flexible, and has excellent washability.
How does DTF printing work?
With DTF technology, you can effortlessly print on various fabrics such as cotton, polyester, blends, synthetic materials, fleece, nylon, and many more without any difficulties. Additionally, Direct-to-Film transfers work great with both dark and white fabrics, eliminating the need for any weeding process, such as vinyls, or the application of A & B paper, as required in white laser toner printing systems.
DTF printing is a simple yet effective printing process that consists of the following steps:
Step 1: Design Creation
The first step in the DTF printing process is design creation. This can be done using a graphic design software like Adobe Illustrator or CorelDraw. The design can also be downloaded from the internet or purchased from a design marketplace. Given the wide range of RIP software options available for DTF printers nowadays, including CADlink, AcroRIP, FlexiPRINT, and others, you can utilize these programs to customize your white base and perform various other editings for your prints.
Step 2: Printing onto Film
Once the design is ready, it is printed onto a clear DTF film using a Direct to Film printer. The printer uses a special ink that is designed to adhere to the film and produce vibrant colors. The printer can print on a variety of films, including PET film, PVC film, and polyurethane film. In the market, you can find a wide variety of films, but to achieve the best quality transfer, it is crucial to stick with high-quality films.

Step 3: Applying Powder to the Printed Film
After the design is printed onto the DTF film, a fine powder specifically designed for DTF printing is applied to enhance the transferring process. This powder acts as an adhesive and helps to improve the adhesion of the ink to the fabric. The powder adheres to the ink and prepares it for the subsequent transfer onto the fabric. Excess powder is gently tapped or shaken off to ensure a clean and precise transfer. This step ensures optimal ink adhesion and contributes to the overall quality of the final print.
Step 4: Transfer onto Fabric
The DTF film is then placed on top of the textile and heat pressed. The heat and pressure cause the ink to transfer from the film onto the fabric, creating a vibrant and durable print.
What are the advantages of DTF printing?
DTF printing offers several advantages over traditional textile printing methods. Some of these advantages include:
- Superior Print Quality: DTF printing produces high-quality prints with vibrant colors, sharp details, and excellent clarity. With DTF specialty inks, the prints will have premium-quality with enhanced brightness and delicacy of color tones on both dark and light fabrics.
- Versatility: DTF printing can be used on a wide range of fabrics, including cotton, polyester, nylon, and more.
- Durability: DTF prints are durable and can withstand multiple washes without fading or cracking.
- Cost-Effective: DTF printing is a cost-effective printing method that requires minimal setup and has low ink costs.
- Fast Turnaround Time: DTF printing is a fast printing method that allows for quick turnaround times, making it ideal for small to medium-sized print runs.

What are the disadvantages of DTF printing?
Despite its many advantages, DTF printing also has some disadvantages. Some of these disadvantages include:
- Limited Color Range: DTF printing is limited in its color range and cannot produce the same range of colors as other printing methods such as sublimation printing.
- Film Costs: DTF printing requires the use of clear films, which can be expensive.
- Image Size Limitations: The size of the design that can be printed onto the film is limited by the size of the printer.
- Special Ink Required: DTF transfer printers require special ink that is not compatible with other printers.
Conclusion
DTF printing is an innovative printing technology that is quickly becoming the future of textile printing. It revolutionized the textile printing industry by providing unmatched convenience and flexibility. DTF transfers offer superior print quality, versatility, durability, and cost-effectiveness compared to traditional printing methods. The efficient process with quick production turnaround opens up endless possibilities for designers and small businesses. While there could be some disadvantages to DTF printing, the benefits far outweigh the drawbacks. As DTF printing technology continues to evolve and improve, it is likely that more textile companies will adopt this technology and use it to create high-quality, vibrant prints that will stand the test of time. This DTF printing is poised to reshape the future of textile printing, offering unparalleled quality and customization options for the printing industry.